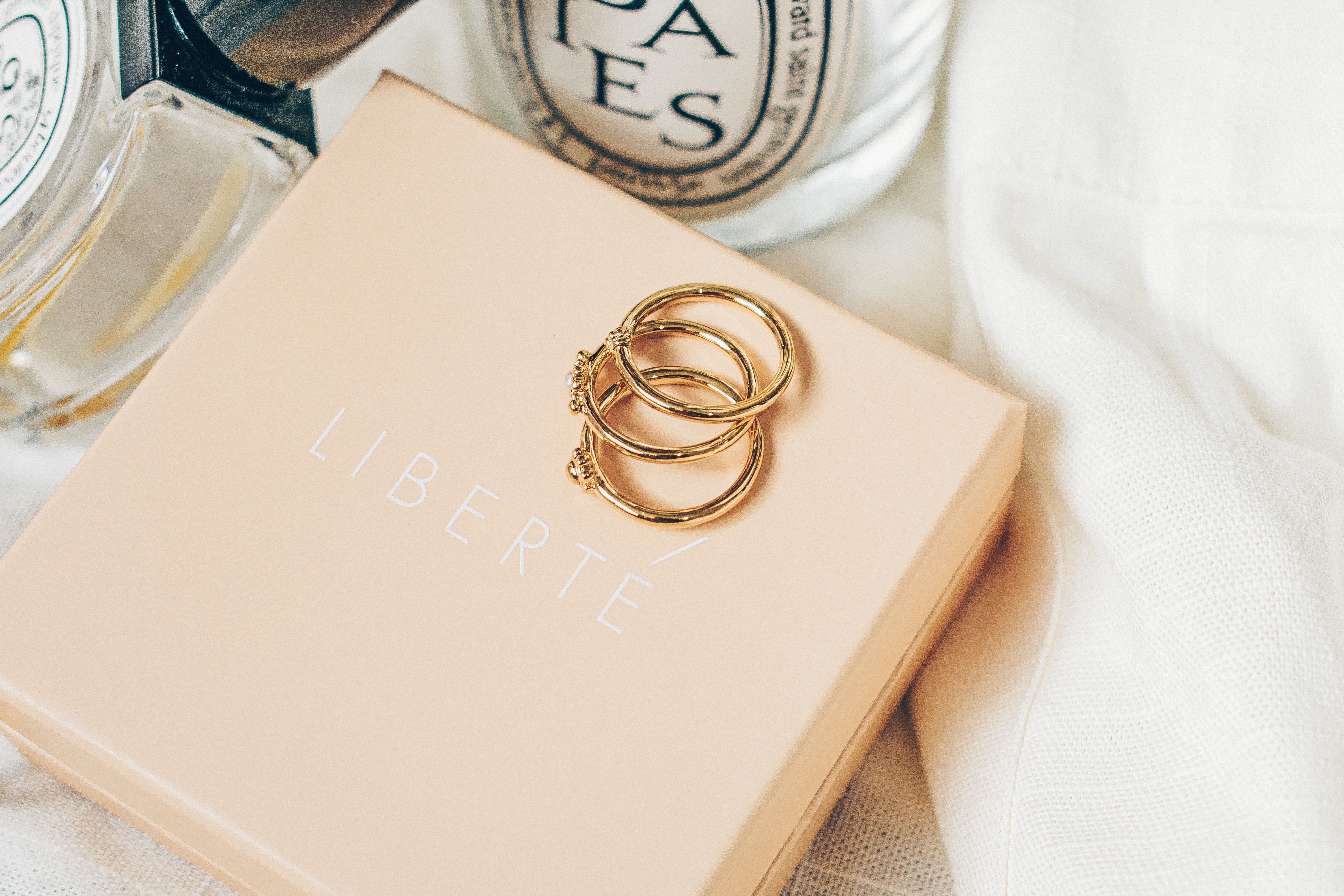
Plating in jewelry is a process whereby a thin layer of a metal is laid over the underlying metal or other material in order to coat and protect it. Plating is used to enhance the appearance of jewelry, inhibit corrosion or tarnishing, and improve wearability.
Types of metal plating
Electroplating
Electroplating is the most common type of plating used in the manufacturing of jewelry. This is a process whereby a coating of one metal is applied to a surface of another metal through the process of electrolysis. In a liquid plating bath, the cathode (the part that will be plated) receives the deposition of the metal from the anode (the part of metal that will be used to form the plating). A continuous electrical charge is applied through the anode and the cathode in the electrolyte chemical bath and the metal is deposited as a result.
Many types of metals can be electroplated in this process. Some examples are gold, silver, tin, zinc, copper, chrome, nickel, platinum and lead.
Electroplating is popular with jewelry manufacturers because the upfront tooling investment costs are lower than more sophisticated alternatives, and the operation of these can be easily mastered by low-level staff. The amount of metal typically applied is very small - referred to as “flash plating” because it is applied so quickly. To apply greater amounts of the plating metal to the plated object quickly becomes expensive as there is no way to ensure the plating is spread evenly, and so to reach “minimum guaranteed” thresholds can be expensive.
Electroplating often leads to consumer disappointment as the plating will easily wear-off, especially on high contact areas like the hands, meaning rings will often discolor very quickly. Equally accidental exposure to swimming pools or sea-water will lead to rapid discoloration.
pen plating
Pen plating, also known as brush plating, is an electroplating technique widely used in jewelry manufacturing. The technique offers several advantages that make it a valuable tool in the jewelry-manufacturing process:
- High precision for plating metal application
- Ability to add very fine details in a plating metal
- Very low metal loss (waste)
- Increase gross light refraction of stones set in metal
- Cost-effective option for small-scale and specialized applications.
- Reduced risk of over-plating
- Provide faster turnaround times for plating jobs, especially when only specific areas need to be plated
This method is commonly used in jewelry manufacturing, repair, restoration work and adding decorative touches to jewelry or other metal objects.
A common manufacturing method in the lower to middle jewelry market is to pen-plate white rhodium around the prongs of a yellow gold diamond cluster ring to increase the overall “sparkle” of the piece as the white metal will reflect more light than if it was left yellow (seen below).
immersion plating
Immersion plating, also known as dip plating or displacement plating. Immersion plating does not require any electricity or external power source in the plating process. This makes for an easy plating set-up and reduces the risk of electrical issues.
Jewelry manufacturers have specific benefits using Immersion plating which can effectively coat jewelry pieces with complex geometries, irregular surfaces, or fine details. This makes it particularly suitable for pieces with intricate patterns, filigree work, or textured surfaces that might be challenging to plate using other methods.
Immersion plating bonds layers of nobler metals (such as rhodium and silver) to the surface of another metal by dipping it into an ion solution of the more noble metal to generate a replacement reaction. This causes a metallic coating to be deposited to the base metal from liquid solutions containing the desired coating metal.
Physical vapor deposition (PVD)
Physical Vapor Deposition plating is a manufacturing technique whereby the material being applied is vaporized in a vacuum, and then deposited onto the surface of the target material, sitting inside the vacuum chamber.
This method is widely used in large scale manufacturing and you can see it all around your everyday life from shiny parts of your car’s dashboard, to children’s toys to door handles and light switches.
PVD plating has many advantages - the amount of material applied is very low, yet the expected life-span of the plating is extraordinarily long, even able to withstand exposure to chlorine and salt-water, enabling commercialization as “water proof plating”. It is widely used in the watch industry where many watches share common parts, and only rarely used in the jewelry industry at the time of writing.
PVD is comparatively expensive tooling to acquire, and requires sophisticated engineers to operate. Further, the process demands a certain batch size which leads to it being more suited to highly repeatable or high volume manufacturing.
e-coating
E-coating is also known as electrocoating or electrophoretic coating. It is a method of painting or coating. E-coating is widely used in various industries such as automotive, electronics, appliances, and jewelry manufacturing.
It is often used as a method of applying a protective and decorative finish to various objects, including jewelry. The e-coating process involves immersing the jewelry pieces in a specially formulated paint or coating solution and applying an electric current to facilitate the deposition of the coating onto the surface. Jewelry manufacturers mainly use the e-coating layer to act as a protection barrier layer against tarnishing, corrosion, and wear. This enhances the overall durability and lifespan of the jewelry, making it well-suited for pieces that are exposed to everyday use and environmental conditions.
E-coating may change the look and feel of whatever metal it is applied to - when done badly it can leave the metal feeling “plastic-like” to the touch. This also depends on variations in coating materials and coating thickness applied, and some e-coating materials may produce a more natural feel compared to others. When done expertly, the consumer will not even notice the difference - except in terms of the extended plating lifetime.
What is a micron?
A micron is a standard unit of measure, measuring one millionth of a meter or one-thousandth of a millimeter (0.001mm). It refers to a unit of measurement for the thickness of a coating or plating applied to a jewelry piece. It is commonly used to describe the thickness of plating. Micron is known by its abbreviation μm.
When discussing micron thickness in jewelry, it typically refers to the thickness of the plated layer. For example, a jewelry piece might be gold plated with a thickness of 0.5 micron. The plating thickness measurement or micron measurement is important because it may affect the appearance, wear resistance, and longevity of the plated jewelry. A thicker plated layer - which means a higher number of micron - generally provides better durability and a longer-lasting finish. Thinner plating may wear off more quickly, exposing the base metal underneath.
What is vermeil?
Vermeil is a specific type of gold-finished material that is involved in the application of precious metals, typically gold, onto a base of sterling silver. In jewelry industry standards, the gold portion must be minimum 10 karats and at least 2.5 microns minimum thickness for a piece to be considered vermeil.
The term "vermeil" is from the French word which historically referred to gilded silver or silver-gilt objects. Vermeil jewelry offers the high expensive look of solid gold jewelry that affordable price, making it a reasonable choice to consumers who want the appearance of high-end jewelry with the lower cost.
Common plating in watches versus jewelry
Watches
Stainless steel is the metal most widely used in luxury wrist-watches, and is often used as a plating material because of its durability and resistance to corrosion. This is due to it boasting many innate properties, including its strength and lightweight feel. It’s also widely available, lowering the cost of the raw material.
Gold plating is a popular choice for its attractive appearance and luxurious feel, and is often used in high-end watches. Silver has a bright, reflective finish and is often used in plating dress watches. Rose gold plating has also been a popular choice for its unique color and fashionable appearance.
PVD is a common type of plating used in watches to create a durable and scratch resistant coating, making it a popular choice for sport and outdoor watches. It can be used to create a range of colors and finishes, such as black or gray, that are not possible with traditional plating techniques.
Jewelry
The main purpose of jewelry plating is to protect the base metal against tarnishing and to give the whole element more decorative qualities. In fashion jewelry, which is typically made from lower cost materials such as base metals, brass, or copper, plating is often used to give the piece a more expensive look.
Common plating materials in fashion jewelry include gold, rose gold, and silver, among others:
- Gold plating is often a popular choice for plating in jewelry, as it lends a luxurious look while being more affordable than solid gold. For this reason, It is often used in fashion and costume jewelry
- Silver is a versatile metal that is often used for plating; it has a bright, reflective finish and can be used to create a range of looks, from classic to modern
- Rhodium plating is often used in fine jewelry. It is a highly reflective and durable metal, and frequently used to plate white gold and platinum in order to enhance their shine and durability
- Platinum plating is used in high-end jewelry to enhance its value and beauty, creating a luxurious and durable finish on jewelry
- Palladium is a less common plating material that is known for its durability and hypoallergenic properties, and therefore is more commonly used in jewelry for people with sensitive skin
Overall, the choice of plating material in both watches and jewelry will depend on the desired look, cost, and durability. Gold plating may be used to make an affordable fashion piece and create a trend, whereas platinum plating may be used to enhance the beauty and value of fine jewelry items.